In the modern industrial world, the demand for efficient, hygienic, and versatile equipment for processing liquids and semi-solids continues to grow. Whether it's in pharmaceuticals, food and beverage, cosmetics, chemicals, or water treatment, the need to blend, mix, and store materials effectively is essential to maintaining quality, safety, and productivity. Among the many solutions available, conical mixing tanks have emerged as a popular and trusted option for many industrial applications. Their distinct design and operational advantages make them a preferred choice for both blending and storage.
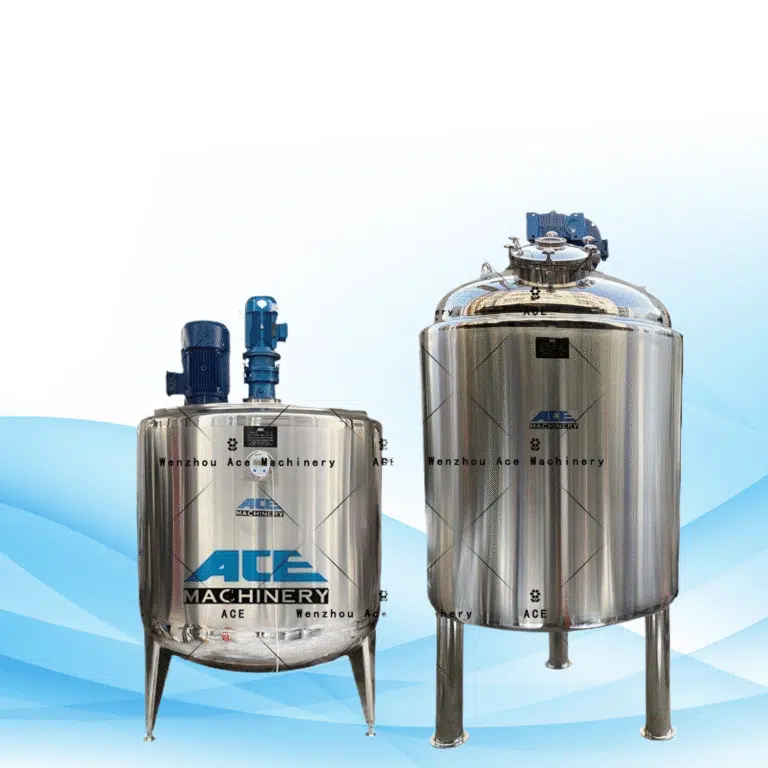
The Unique Design of Conical Mixing Tanks
Conical Mixing Tank are characterized by their cylindrical body and cone-shaped bottom. This cone design is more than just a structural feature—it plays a central role in improving mixing performance and enhancing product drainage. The sloped bottom naturally guides liquids and solids toward the center outlet, making these tanks highly effective in achieving uniform blending and complete discharge.
The design is also compatible with various types of agitators and mixers, allowing customization based on the materials being processed. Whether the goal is to dissolve powders, suspend solids, or mix viscous fluids, the geometry of a conical tank supports better fluid dynamics than flat-bottom tanks, which often have dead zones or areas of poor flow.
Improved Mixing Performance for Better Product Quality
One of the most important reasons industries prefer conical mixing tanks is their ability to produce consistent and homogenous mixtures. The conical shape facilitates a natural flow of materials downward, allowing for better circulation during mixing. As the agitator moves the contents, the design ensures that materials are constantly pushed back into the mixing zone, reducing the likelihood of unmixed pockets.
This level of mixing performance is especially important in industries where product consistency is critical. In pharmaceuticals, for example, a uniform blend of active ingredients ensures that each dose has the correct potency. In food production, thorough mixing contributes to flavor, texture, and safety. Even in chemical manufacturing, proper blending prevents reaction inconsistencies and improves yield.
Efficient Drainage Reduces Waste and Simplifies Cleaning
The cone bottom of these tanks is not only beneficial during mixing but also during discharge. The sloped design allows gravity to naturally assist in draining the contents toward the bottom outlet. This feature is particularly useful when dealing with viscous or sticky substances that might otherwise cling to the walls of a flat-bottom tank.
With better drainage, there is less residual product left behind. This minimizes waste, ensures higher recovery of valuable materials, and reduces the time and effort needed to clean the tank between batches. In applications where hygiene is critical, such as in the food and pharmaceutical industries, this complete drainage helps reduce contamination risks and supports quicker turnaround times.
Versatility in Industrial Applications
Conical mixing tanks are highly adaptable and serve a wide range of industrial needs. In the food and beverage industry, they are used to blend ingredients like sauces, dairy products, syrups, and juices. In pharmaceuticals, they handle sensitive compounds that require precision and cleanliness. In the chemical sector, they are used to process corrosive materials, polymers, and solvents under controlled conditions.
The tanks can be manufactured in various materials such as stainless steel, polyethylene, or fiberglass, each selected based on the chemical compatibility and processing requirements. They are also available in multiple sizes, from small laboratory-scale units to large production vessels, making them suitable for everything from research and development to full-scale manufacturing.
Support for Temperature Control and Specialized Features
Many industrial processes require temperature control to ensure proper reaction rates or to preserve the integrity of ingredients. Conical mixing tanks can be equipped with jackets for heating or cooling, allowing operators to maintain precise thermal conditions throughout the mixing process. This is particularly important in chemical reactions, fermentation, or temperature-sensitive blending.
Other specialized features, such as pressure resistance, insulation, sight glasses, and digital monitoring systems, can be added based on the application's needs. These enhancements improve safety, provide better process visibility, and support automation in modern production environments.
Ease of Integration into Production Systems
Another reason industries favor conical mixing tanks is their ease of integration into existing production lines. Their standardized connections and fittings allow them to be easily linked with other equipment such as pumps, filters, filling machines, or CIP systems. This flexibility enables manufacturers to design streamlined and efficient workflows that reduce labor and processing time.
Moreover, many conical tanks are designed for mobility. They can be mounted on skids or fitted with wheels, allowing them to be moved from one location to another within a facility. This mobility makes them especially useful in operations that require multiple processing steps or small-batch production.
Cost-Effectiveness and Operational Efficiency
While the initial investment in a high-quality conical mixing tank may be higher than simpler alternatives, the long-term benefits justify the cost. These tanks reduce product loss, shorten processing and cleaning time, and support faster batch turnaround. The reduced need for manual cleaning and handling lowers labor costs and minimizes downtime.
Over time, the increased productivity and material savings provided by conical tanks contribute to lower operational costs. Additionally, the durability and low maintenance requirements of well-constructed tanks—especially those made from stainless steel—translate into a longer service life and better return on investment.
Compliance with Industry Regulations and Standards
For industries such as food, beverage, and pharmaceuticals, regulatory compliance is not optional. Conical mixing tanks are often built to meet strict standards for hygiene, safety, and traceability. Stainless steel tanks, in particular, can be manufactured to comply with FDA, GMP, 3A, and other sanitary requirements.
Tanks can also be customized with certification for pressure or vacuum operation, corrosion resistance, and traceable manufacturing processes. These compliance features not only ensure safety and quality but also make inspections and audits smoother and more efficient.
Sustainability and Environmental Benefits
Sustainability has become a key focus for modern industries. Conical mixing tanks contribute to environmental goals by reducing product waste, minimizing energy use, and facilitating easier cleaning with less water and detergent. The ability to recover nearly all of the product in each batch means less raw material is wasted, which is especially important when handling expensive or sensitive ingredients.
By improving process efficiency and reducing resource consumption, conical tanks help industries move toward greener and more sustainable operations. For companies focused on reducing their carbon footprint and meeting environmental standards, the switch to conical tanks is a practical and impactful step.
Conclusion
Industries across the board are turning to conical mixing tanks for their blending and storage needs due to the many advantages these tanks offer. Their unique shape enhances mixing performance, ensures complete drainage, supports sanitation, and simplifies integration into modern processing systems. With versatility across materials and sizes, the ability to handle temperature and pressure requirements, and compliance with regulatory standards, conical tanks are an ideal solution for industrial applications.